591views
Trade disputes are not a rare sight in the current competitive era. Especially the USA and China have a history of such disputes in last couple of decades and both have locked horns again, this time over solar equipment trade. Chinese manufacturers are being accused of unfair trade practices as they sell solar modules at a considerably lower prices than producers from other countries, using government subsidies to finance their operations and to create a glut of imports. In response to such a practice, American manufactures filed a petition with US International Trade Commission (USITC) seeking steep tariffs and a floor price for the Chinese solar imports. The commission voted on the merits of the petition in late September 2017, and decided that there has indeed been a considerable damage to the US manufacturers. The USITC’s recommendations for sanctions will be sent to the White House to decide the course of action in the following month. If sanctions are introduced, will the US producers be the ultimate winner after the final verdict in November?
The solar power generation technology was invented in the USA which have dominated the solar industry for last three decades of 20th century. The global solar industry is now a US$100 billion market, a fact that leads to a large number of players being interested in grabbing their share of this mammoth opportunity. As solar energy is considered clean and renewable, countries suffering from high pollution levels increasingly demand efficient and cheap solar energy generation equipment.
This strong demand is expected to continue, luring many players around the globe towards venturing into solar equipment manufacturing and this in turn has led to intense competition in this market. With China rising as a manufacturer of cheaper solar equipment since 2011, it has become increasingly difficult for other players to compete with China, and many producers, especially in the USA, are not very pleased with that.
This strong demand is expected to continue, luring many players around the globe towards venturing into solar equipment manufacturing and this in turn has led to intense competition in this market.
This is not the first solar battle between the USA and China. The countries were in a solar dispute back in 2011 when the USA hit China with 25-70% tariffs on solar module exports. It was due to a trade complaint filed by SolarWorld Americas along with six other US manufacturers about unethical trade practices undertaken by their Chinese counterparts. And now, Suniva, a Georgia-based solar cell and module manufacturer, filed a Safeguard Petition with the USITC in April 2017, just one week after it had filed for chapter 11 bankruptcy.
The USITC, in its unanimous vote, agreed that the US companies suffered injury from cheap imports. Following these developments, the markets are waiting for the president Trump’s decision over the case in November, and if the White House follows with sanctions and remedies, this might be the beginning of a significant wave of changes in the solar equipment market.
China has not always been the market leader for solar products. Way back in 1990s, when Germany could not meet its rising domestic demand for solar equipment, it started working with Chinese players to manufacture the equipment for German market. Germany did not only provide the capital and technology but also some of their solar energy experts to those Chinese manufacturers.
The high demand was a result of German government’s incentive program to use the rooftop solar panels. Needless to say, those Chinese players happily accepted the opportunity. Further they got lured with the rising demand for solar equipment in other European countries such as Spain and Italy, where similar incentive programs started to be rolled out. The Chinese producers started hiring experts and expanding their capacities to tap the surge in demand.
With rising pollution levels and global demand for cleaner energy, solar industry became an attractive opportunity for China, and this resulted in the government’s willingness to invest as much as US$47 billion to develop China’s solar industry. With the beginning of 21st century, China started inviting foreign companies to set up plants in the country and take benefit of its cheap labor.
The Chinese government also introduced loans and tax incentives for renewable energy equipment manufacturers. By 2010, the solar equipment production in China increased at such levels that there were almost two panels made for every one demanded by an importer. In 2011, China took the German route and started incentivizing domestic rooftop solar installations, which rocketed the domestic demand so much that it surpassed Germany’s in 2015 to become the largest globally. China deployed 20 GW capacity in the first half of 2016, whereas the entire US capacity at that time was 31 GW.
The Chinese government started perceiving solar power generation as a strategic industry. It started a range of initiatives to help the domestic manufacturers to increase production of solar equipment, be it through subsidies for the purchase of the land for factories or through lower interest loans from banks. These moves and gigantic Chinese production capacities drove the global solar panel prices down by 80% from 2008 to 2013, which further increased China’s exports as its prices were the lowest.
Before 2009, the USA used to import very little from China in the solar domain and by the end of 2013, the Chinese imports rose to over 49% of total solar panels deployed in the USA. This increase in the imports resulted in 26 US solar manufacturers filing for bankruptcy in 2011, one of which was SolarWorld which also filed a trade complaint. The situation was not very different in several European countries.
The Chinese government started perceiving solar power generation as a strategic industry. It started a range of initiatives to help the domestic manufacturers to increase production of solar equipment.
China was accused of unfair trading and dumping exports below market prices which led the Obama government and EU to imposing import duties of 25-70% on Chinese solar products in 2011 for the following four years. In return, in 2012 China threatened to impose tariffs on US imports of polysilicon used in solar cells, and actually announced tariffs of 53.5% to 57% in 2013. Also, finding loopholes in the tariff system imposed by the Americans, Chinese manufacturers set up facilities in countries such as Malaysia and Vietnam, as the tariffs were not applicable for imports from those countries. The US imports of Chinese solar products continued.
The current Suniva’s case has received a mixed support within the US solar industry. While the US solar installers, for obvious reasons, will not support the case, some of the well-known manufacturers in the country have also stood up against it. They think the tariffs will almost double the prices of solar equipment in the USA which will eventually lower the demand of their products as well.
Following the USITC vote agreeing with Suniva’s petition, the industry is awaiting the final decision on the extent of the recommended tariffs and remedies, which are expected to affect jobs, innovation, and growth of the solar industry in various ways.
Impact of tariff decision on jobs in solar industry
Out of the total 260,000 US solar jobs, installers accounted for more than 80%, and around 38,000 people were working in manufacturing in 2016, a 26% increase over 2015. As the prices of solar panels dropped to around US$0.4/watt in 2016 from US$0.57/watt in 2015 thanks to the availability of cheap Chinese imports, solar installations boomed in the USA.
Manufacturers and experts supporting the Suniva case (supporters) argue that if the suggested tariffs of US$0.4/watt on imported cells and a minimum price of US$0.78/watt on panels are implemented, it will help the domestic manufacturing and around 114,800 new jobs will be created. The installers and some manufacturers opposing the case (adversaries) say that the tariffs on import will hurt everyone including the manufacturing sector. If the prices increase, this will cause the demand to go down which is likely to affect around 88,000 jobs in the US solar industry.
A group of 27 US solar equipment manufacturers including companies such as PanelClaw, Aerocompact, IronRidge, SMASHsolar, Pegasus Solar, on behalf of their combined 5,700 employees, wrote a letter to trade commissioners not to impose new import tariffs. With Chinese solar imports as high as 49% of the total US requirement, increased prices are expected to affect thousands of jobs in the solar installation sector which is the primary sub-sector of solar industry.
However, if the Chinese imports continue at the current rate, the demand for solar equipment will eventually decrease. Over long term, the manufacturers will have to lower their production and installers will have no new clients. So, the economy of scale effect will not work after that and that might affect the US solar jobs.
Impact of tariff decision on innovation in solar industry
The one factor that genuinely seems affected with the rise of China in the solar industry is innovation. Being the pioneers of the solar power generation technology, Americans are undoubtedly good at innovation. However, with dozens of US companies being on the verge of bankruptcy and lowering sales for remaining manufacturers because of glut of cheaper Chinese imports, the innovation budgets have seen a large blow in the country.
China is still producing the first generation, traditional solar modules and doing little, if anything at all, to improve the efficiency of the existing products. Chinese are not known for investing much in R&D departments and top seven Chinese solar manufacturers invested a mere 1.25% of total sales in R&D in 2015. Compared with what electronics firms invested in 2015 towards R&D, this number is six times lower. Compared with US clean energy firms, Chinese firms patent 72% less.
However, the US innovation receives targeted help and support from the government, which is not the case for Chinese innovation. US Department of Energy has come up with a loan program of US$32 billion to help clean energy companies innovate efficient solar products while still being price competitive with Chinese products. Nonetheless, US innovations are expected to dry up if the Chinese solar equipment dumping continues.
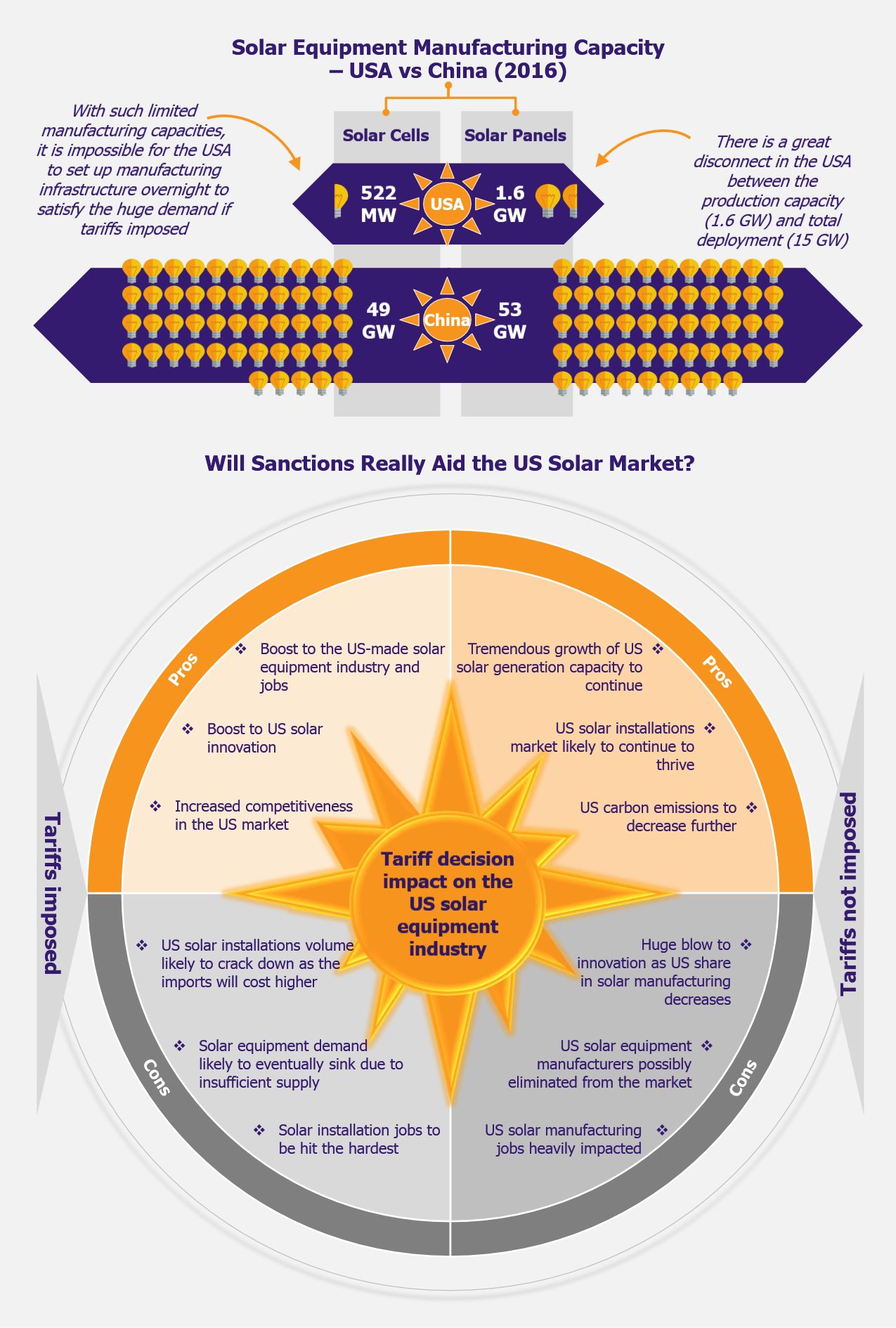
Impact of tariff decision on solar industry growth
Growth of the solar industry should probably be the prime factor to consider for the Trade Commission and the White House while deciding about the potential introduction of solar tariffs.
As of 2016, US solar industry is worth roughly around US$23 billion. Moreover, solar energy accounted for 40% of new generation in the US power grid and 10% of total renewable energy generated in the USA in 2016, while the recent cost declines have led American utilities to procure more solar energy. This energy has witnessed 68% of average annual growth rate in terms of new generation capacity in the USA in last decade and as of first half of 2017, over 47 GW of solar capacity is installed to power 9.1 million American houses. There are currently about 9,000 solar companies in the USA employing around 260,000 people. In 2016, solar power generation was at 0.9% of total US power generation, a share that is expected to grow to more than 3% in 2020 and hit 5% in 2022.
The Suniva case supporters believe that this growth can slow down once the solar equipment demand is satisfied through Chinese imports, which is likely to eventually lead to job cuts and no innovation that in turn will put a break on any further growth in the US sector. They also argue that the solar equipment manufacturing sector in the USA will be destroyed if the right steps are not taken to safeguard the manufacturers from cheaper imports.
After the tariffs are introduced, for some time, the prices will be parallel for locally manufactured as well as imported solar products. Later on, with innovation and competitiveness between the domestic manufacturers coming back (currently absent from US solar market), the prices are expected to go down as per the allies.
At the same time, the Suniva case adversaries believe that the dream run for solar industry’s growth in the USA should not be hindered by imposing tariffs on imports as it will jeopardize even up to half of all solar installations expected to be demanded by 2022. In case of US$0.78/watt minimum module price scenario, US solar equipment installation is expected to fall from 72.5 GW to 36.4 GW between 2018 and 2022 or to 25 GW in case of US$1.18/watt minimum price scenario.
Solar energy is believed to be price sensitive and if the government aims to motivate the clean energy development, the origin of equipment used for this development should not matter. Some of the US solar equipment manufacturers are even opposing the tariffs which means they think there is still potential in the domestic manufacturing industry and with innovation they can gradually increase their share in the market.
EOS Perspective
The US government will have to take a responsible decision on the trade tariffs. The issue looks very sensitive and can directly affect the growth of the US energy sector. A win-win situation seems impossible if the tariffs are levied, and in its deliberations the government should consider the effects of the past US tariffs imposed on Chinese products. When the USA took anti-dumping steps against Chinese steel, China fired back with tariffs on caprolactam, a textile material. China re-imposed duties on US broiler chickens, after the USA announced duties on Chinese tires in June 2015.
So, none of the trade wars have proved to be beneficial for either of the sides. In the current dispute, the stakes are also high, and the wrong decision might have repercussions in a range of sectors. For instance, China placed a US$38 billion order to Boeing for commercial aircraft in 2015, an order that has not been delivered yet. This aspect should be kept in mind by the USA.
China currently dominates solar products supply with 80% of global solar equipment manufacturing capacity. The USA need to understand that their role in the global solar market is decreasing, and is no longer what it used to be. It would be beneficial for the USA to focus on strengthening the role in innovation of solar technology rather than looking to be the leading solar equipment manufacturer by volume.
Even if the US government supports the manufacturers by slapping tariffs on imports, the country is not ready with the required infrastructure for solar generation equipment manufacturing to satisfy the domestic demand in absence of the imports from other countries. Solar equipment producers cannot instantly set up infrastructure to manufacture a number of solar products, such as solar cells, junction boxes, extruded aluminum, glass, etc., that too in a cost-effective model. President Trump’s support for reviving local manufacturing, while at the same time favoring fossil fuels over the green energy (also manifested through his withdrawal from Paris Climate Accord), makes the outcome of the case uncertain, and interesting to follow.